1. 관리도 필요성, 구성 요소, 적용절차
공정을 안정적으로 관리하는 도구에는 여러 가지가 있지만, 가장 기본적인 방법은 중요한 특성의 변화를 지속적으로 모니터링하는 것이다. 예를 들어, 값이 상승하거나 하락하는 추세를 보이거나 갑작스럽게 변동이 발생하면, 이를 이상 현상으로 판단할 수 있다. 그렇다면 이러한 변화가 정상적인 변동인지, 아니면 이상 현상인지 어떻게 판단할 수 있을까? 관리도가 그 기준을 제시한다.
관리도(Control Chart)는 공정의 변동을 시각적으로 감시하고 이상 여부를 판단하는 데 사용되는 대표적인 통계적 품질 관리 도구이다. 이를 통해 공정이 정상적으로 운영되고 있는지, 아니면 이상 원인으로 인해 변동이 발생하는지를 판별할 수 있다.
관리도의 역사는 100년 가까이 되었다. 1920년대 미국의 통계학자 월터 슈하트(Walter A. Shewhart)에 의해 개발되었다. 당시 벨 연구소(Bell Labs)에서 근무하던 슈하트는 공정 변동을 분석하고 통제하는 방법을 연구하면서 관리도의 개념을 정립하였다. 그는 1924년에 최초의 관리도를 개발하였으며, 이를 기반으로 1931년 『경제적 품질 관리(Economic Control of Quality of Manufactured Product)』라는 저서를 출판하여 관리도의 개념과 활용법을 체계적으로 정리하였다. 이후 관리도는 공정 품질 관리의 핵심 도구로 자리 잡았으며, 1950년대에는 일본의 데밍(W. Edwards Deming)과 주란(Joseph M. Juran) 등이 이를 발전시키며 품질 관리 기법을 전 세계로 확산시켰다. 현재는 제조업뿐만 아니라 다양한 산업에서 활용되고 있으며, 지속적인 품질 개선과 공정 최적화를 위한 필수적인 도구로 자리 잡고 있다.
필요성
공정은 설정한 값대로 똑같이 생산되지 않고, 변동(Variation)또는 산포가 존재한다. 이 변동은 일반적으로 두 가지 원인으로 구분된다.
- 우연 (공통)원인 변동(Random/Common Cause Variation): 공정 내에서 자연스럽게 발생하는 변동으로, 시스템 내의 정상적인 요소로 간주된다.
- 이상 (특별) 원인 변동(Abnormal/Special Cause Variation): 특정 사건이나 변화로 인해 발생하는 비정상적인 변동으로, 이를 찾아 제거하지 않으면 품질 문제가 발생할 수 있다.
관리도를 사용하면 이러한 변동을 감시하여 공정이 안정적인지 여부를 판단하고, 필요할 경우 적절한 조치를 취할 수 있다.
이상 원인을 판정하는 기준은 일반적으로 정규분포의 3시그마(σ) 범위를 벗어나는 경우이며, 이때 발생할 확률은 약 0.27%이다.
즉, 공정이나 검사 과정에서 채취한 샘플(표본)의 평균이 3시그마 선 밖에 위치할 경우, 이를 이상 원인에 의한 변동으로 판단한다.
여기서 중요한 이론적 근거는 중심극한정리이다. 이 정리에 따르면, 모집단의 분포 형태와 관계없이, 표본의 평균은 정규분포를 따르게 된다.
따라서 공정 데이터가 정규분포가 아니더라도, 표본 평균을 기준으로 한 관리도를 사용하는 것이 가능하다.
아래는 정규분포에서 표준편차(σ) 수준별로 해당 구간에 속할 확률을 나타낸 것이다.
±3σ 이내에 존재할 확률은 99.73%, 이를 벗어날 확률은 0.27%로 나타난다.
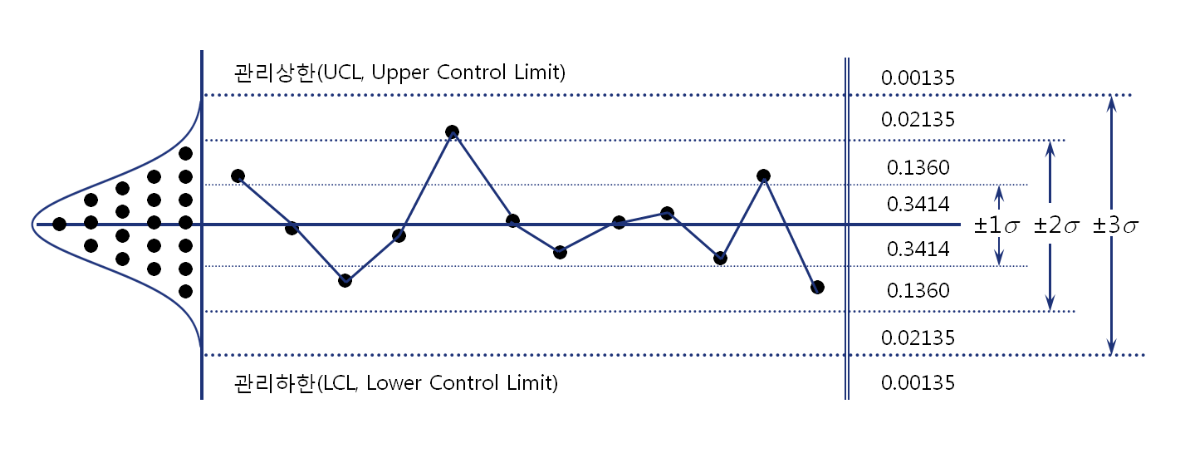
일반적 환경에서 발생 확률이 0.27% 되지 않는데, 이러한 Case가 발생되었는데 확인하지 않고 넘어 갈 수가 있겠는가?
그러면, 무엇을 확인 할 것이가? Output에 영향을 미치는 Input 5M +1E 요소를 확인한다.
- Man (사람) – 작업자의 숙련도, 실수, 교육 부족, 피로 등
- Machine (설비) – 기계의 고장, 오작동, 유지보수 부족 등
- Material (재료) – 원자재 불량, 규격 미달, 오염 등
- Method (방법) – 작업 절차 오류, 공정 조건 불량, 표준 미준수 등
- Measurement (측정) – 측정 방법 오류, 측정기 오류 등
- Environment (환경) – 온도, 습도, 조도, 소음 등 외부 환경 요소
이상이 발생했을 때 하나씩 개별적으로 확인하는 것은 어렵기 때문에, 일반적으로 Control Plan(QC 공정도)를 수립할 때 특정 특성에서 이상이 발생하면 확인해야 할 사항을 미리 정해둔다. 미국 National Semiconductor의 Fab 공정을 방문하여 관리도 이상 조치 방법을 확인했을 때, Operator는 화면에 차례로 표시되는 12~14개의 체크 항목을 하나씩 점검한 후에도 원인을 파악하지 못하면 “확인 안 됨”으로 기록하고 현장에서 넘어갔다. 이후 Engineer가 추가로 근본 원인을 분석하는 방식으로 운영되고 있었다.
구성 요소
관리도는 일반적으로 세 가지 주요 요소로 구성된다.
- 중심선(Central Line, CL): 공정의 평균값을 나타낸다.
- 상한 관리한계(Upper Control Limit, UCL): 공정 변동이 정상 범위를 벗어나는지를 판단하는 상한선이다.
- 하한 관리한계(Lower Control Limit, LCL): 공정 변동이 정상 범위를 벗어나는지를 판단하는 하한선이다.
이 세 가지 요소를 기준으로 데이터를 시각적으로 분석하여 이상 여부를 판단할 수 있다.
아래 그림은 대표적으로 사용되는 x평균과 R관리도이다. 관리도의 해석은 아래 산포 관리도부터 판정하고 평균 관리도 순으로 확인한다.
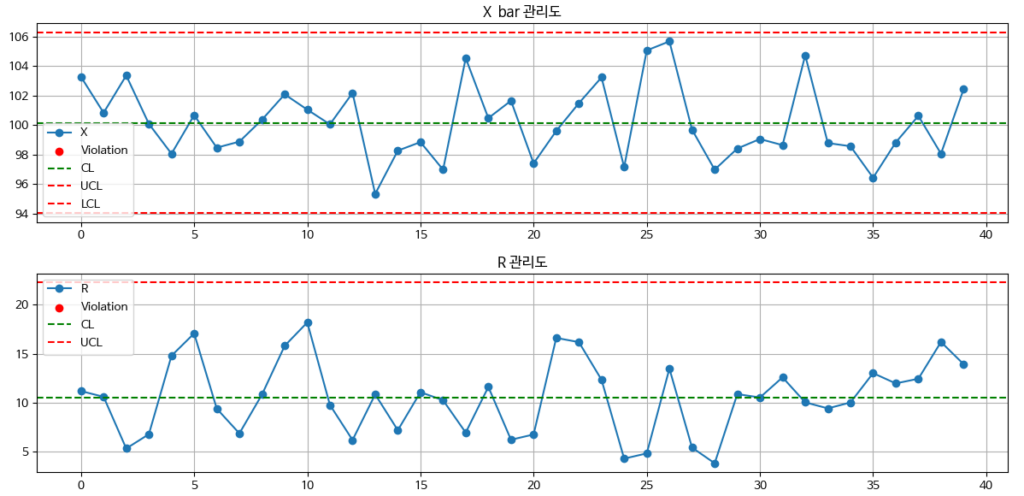
관리도는 작성하기 전에 고려해야 할 요소로는 변동이 파악 할 수 있는 적절한 척도를 가져야 하며, 부분 군 순서/ 스케줄에 따라 데이터가 기록되어야 한다.
또한 해당 작업이 행해 지는 Log들이 파악되어야 한다. 예를 들어 어떤 설비의 어떤 제품, 어떤 Lot이 투입되었는지 등이 기록되어야 이상원인을 추적할 수 있다.
또한 관리도에는 무엇을(부품, 제품) ,어디서(공정 및 제조 설비), 누가(작업자), 어떻게 (검사 설비 또는 계측기), 부분 군 크기, 샘프링 방법 등이 함께 기록 되어야 한다.
이상 판단 규칙
이 관리도를 이상 판정하는 기준은 단순히 3시그마선을 벗어난 기준외에 여러 가지 기준이 존대하는데, 이를 7가지 규칙(7 Rules) 또는 웨스턴 일곱 규칙(Western Electric Rules)이라고 부른다. 기준은 다음과 같다.
- 1점이 중심선에서 3σ 이상 벗어남
- 연속 3점 중 2점이 같은 방향으로 2σ 이상 벗어남
- 연속 5점 중 4점이 같은 방향으로 1σ 이상 벗어남
- 치우침 : 연속 7점이 중심선 한쪽에만 존재
- 경향 : 연속 6점이 증가 또는 감소 (추세 발생)
- 연속 14점이 상승·하강 반복 (비정상적 패턴)
- 연속 3점 중 2점이 2σ 이상 벗어나며 교차
※ 자동차 업계에서 사용하는 기준을 8가지가 있고, 위 기준과 차이가 있다.
( 중심선에서 표준편차 1이내에 일렬로 점 15개, 중심선에서 표준편차 1이사 일렬로 점 8개 추가)
이 규칙을 해당하면 공정 이상 가능성이 높아 확인이 필요하다. 그러나 이러한 기준 적용은 한번에 적용하기 보다, 공정의 관리 능력에 따라 탄력적으로 운영해야 한다. 처음에는 3시그마 기준을 먼저 적용 후 공정관리 능력이 향상되었을때 치우침, 연속적 상승, 하강, 연속 14점의 상승, 하강 반복 등의 기준을 추가하며 관리한다.
관리도 선택
관리도를 선택 할때 데이터의 속성에 따라서 연속형(예: 무게, 치수)관리도와 이산형(예 불량율, 불량갯수, 결점수) 관리도로 구분하여 선택하여야 한다. 아래 그림은 미니탭 보조도구에서 제공하는 그림으로 선택하는데 도움이 된다.
계수치(연속형) 데이터의 부분군으로 구분할 수 없을 때는 I-MR (Individual-Moving Range Chart, 개별값-이동범위) 관리도를 사용하며,
부분군의 크기가 적을 때는 Xbar – R 관리도, 부분군의 크기가 8이상일 때는 X bar -S 관리도를 사용한다. 제조 공정에서 가장 많이 사용하는 관리도는 X̄bar- s 관리도이다. 일반적으로 부분군의 크기가 작을 경우 R 관리도를 사용한다고 하지만, 자동으로 계산하는 시스템이 보편화되어 있어 굳이 R 관리도를 선택할 필요는 없을 것이다. 다만, 매일 손으로 차트를 작성해야 한다면 간편한 계산을 위해 R 관리도를 사용할 수도 있다.
취급하는 데이터가 계수형(이산형) 데이터인 경우 불량율은 불량율 관리도(Proportion Chart)를 사용하고, 샘플갯수가 고정되어 있을 때는 np관리도(불량개수, Number of Defectives Chart)를 사용한다. 결점수 (ex 화면의 defect 갯수, 흠집)의 경우에는 제품 전체의 결점을 계산하는 c 관리도(결점수, Count Chart)를 사용하거나 단위당 결점수로 계산(ex, 면적당 defect 개수)의 경우에는 u 관리도(단위당 결점수,Unit Chart)을 사용한다.
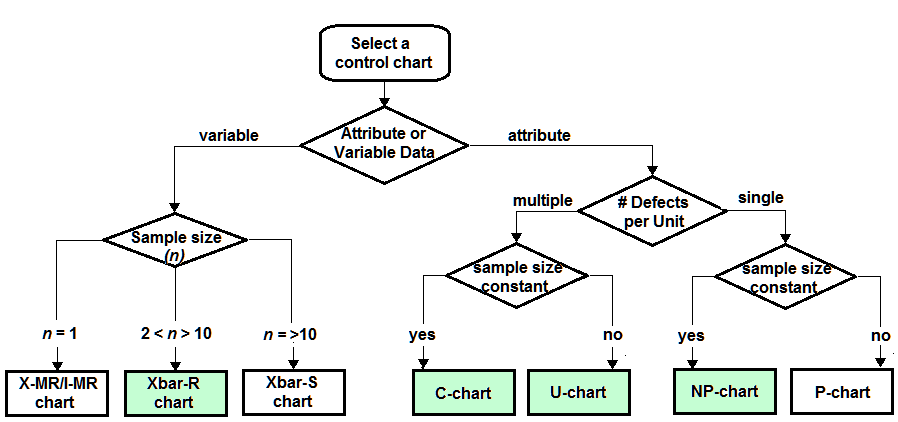
이외에도 최근 데이터에 가중치를 부여하는 EWMA(Exponentially Weighted Moving Average) Chart, 개별 점보다 누적된 변화를 감지하여 작은 변화도 감지하는 CUSUM (Cumulative Sum Control) 관리도, 다변량 데이터를 관리하는 T2(Hotelling’s T² Control) 관리도 등도 있다. 변수가 많을 때 일일히 관리도를 그리기 보다 변수간의 상관 관계가 존대하는지 확인 후 PCA((Principal Component Analysis, 주성분 분석)을 통해 차원을 축소한 후 T2 관리도를 적용 할 수 있다.
한편, 불량률 관리도는 주로 불량이 다발 한 이후에 파악이 되기 때문에 예방 활동을 위한 통계적 관리 Tool로는 적절해 보이지 않고 계수치 Data의 특성상 많은 정보도 가자고 있지 않다. 통계적 공정관리는 가능하면 계량치 Data로 취급하는 것이 우선 되어야 할 것이다.
적용 절차
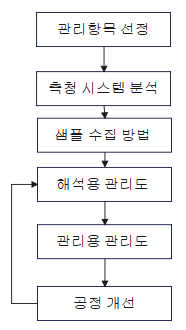
관리도를 적용하기 위해서는 먼저 관리할 항목을 선정해야 한다. 이를 위해 과거의 실패 사례나 공정 FMEA를 분석하여 적절한 관리 항목을 결정한다.다음으로, 해당 항목을 측정하기 위한 측정 시스템을 분석 하여 수용 가능한 수준인지 파악, 샘플(부분군)의 구분 방식을 정한다. 샘플은 대표성을 가질 수 있도록 선정해야 한다. 부분 군간의 변동과 부분 군내의 변동이 구분되도록 설정되어야 한다. 이후 일정 기간 동안 데이터를 수집하여 해석용 관리도를 작성하고, 공정이 관리 상태인지 및 공정능력 수준을 평가한다. 공정능력이 1 미만이라면 Spec 상·하한선을 함께 고려해야 한다.이상치가 발견되면 개선 조치를 수행하거나 해당 데이터를 제거한 후 다시 해석용 관리도를 작성한다. 관리 한계를 수립하는 개별 데이터는 100개 이상, 부분군의 수는 25개 또는 그 이상으로 하여 관리도에 적용할 UCL(Upper Control Limit)과 LCL(Lower Control Limit)을 결정하며, 주기적으로 관리 한계를 재조정한다.또한, 공정이 변경되거나 개선이 이루어지면 해석용 관리도를 다시 작성하고, 새로운 UCL과 LCL을 계산하여 관리도에 반영해야 한다.
관리용 관리도에서 이상이 발생 했을 때의 조치 방법도 사전에 결정해야 한다. 모든 항목을 동일하게 처리하기 보다 등급을 나누어 처리하는 것을 권장한다.
A 등급의 해당 설비생산을 중단하고 확인, B 등급은 해당 Lot을 Hold, C 등급은 그냥 Flow하고 해당 이상을 확인 조치하는 것 등으로 각 제조 상황에 맞게 수립하여 운영해야 한다. 보통 품질 사고가 발생하면 해당 항목에 대해 관리 등급이 강화하여 운영하겠다고 대책이 수립되게 된다.
관리도는 제조 현장에서 필수적인 품질 관리 도구로 자리 잡고 있으며, 고객사 요구나 각종 인증을 위해 반드시 활용해야 하는 중요한 도구이다.
그러나 제조 현장에서 관리도를 적용하는 과정에서는 여러 어려움이 따른다. 특히, 규격을 벗어나지 않았음에도 원인을 분석하고 조치를 요구하는 경우, 현장에서는 반발이 발생할 수 있다. 또한, 관리도를 작성하려면 제품별, 설비별, 계측기별 따로 작성해야 하기에 각각 구분해서 데이터를 수집하고 기록해야 하며, 이상을 검출하기 위한 시스템을 구축하거나 수작업으로 관리도를 작성해야 하는 번거로움이 있다.
이러한 어려움을 극복하고 형식적이 아닌 실제적인 공정관리 도구로 되기 위해서는 제조 또는 품질 책임자는 정기적으로 운영 상황을 들여다 보고 부족한 부분에 관심을 두어야 하며, 여기에서 품질 담당자의 역량이 중요하다. 교육하고, 관련 담당자를 만나고, 설득하고, 적용하고, 잘 운영되는지 확인하는 과정을 반복하며 통계적으로 공정을 관리하는 문화가 정착되어 간다.
관리도를 통해 공정이 정상적으로 운영되고 있는지 지속적으로 모니터링하면, 품질 문제를 사전에 예방할 수 있다. 이것을 적용하는 도구는 현장 상황에 맞게 엑셀 양식을 사용하거나, 공개 또는 상용 통계 프로그램을 사용하여 적용하고 있다. 이러한 프로그램은 실시간으로 반영되지 않고, 사후적으로 파악되기에 개선을 위한 통계적 공정관리보다 기록을 남기는 목적으로 운영되기가 쉽다.
공정 관리도를 위한 실시간 관리도 타점은 필수적인 요소이나 기존 도구로는 쉽지 않다.
향후 포스트에서는 관리도의 이론 바탕으로 파이썬으로 등록된 데이터를 실시간으로 처리하고, 관리도 작성되며, 이상이 파악하는 방법을 다루고자 한다.
관리도별 CL, UCL, LCL 계산 공식 요약 정리표
관리도 종류 | CL (중심선) | UCL (상한 관리 한계) | LCL (하한 관리 한계) |
---|---|---|---|
X̄ 관리도 | |||
R 관리도 | |||
s 관리도 | |||
p 관리도 | |||
np 관리도 | |||
c 관리도 | |||
u 관리도 |
📌 설명
- k : 샘플 개수
- n : 각 샘플당 데이터 수
: 표준 관리도 상수
: F-분포 값
💡 LCL이 음수이면 0으로 설정하는 것이 일반적 (특히 p, np, c, u 관리도의 경우).